
The UK’s leading drywall supplier
Drywall Pro-Cut are rapidly developing the concept of manufacturing drywall components offsite and have become a major UK supplier.
Constantly developing new products, Drywall Pro-Cut have several protected patents for existing products.
Drywall Pro-Cut
With a dedication to innovation, we continuously expand our product range and hold multiple patents to protect our unique developments.
Leading the way in offsite drywall component manufacturing, the company is rapidly growing and has become a major UK supplier.
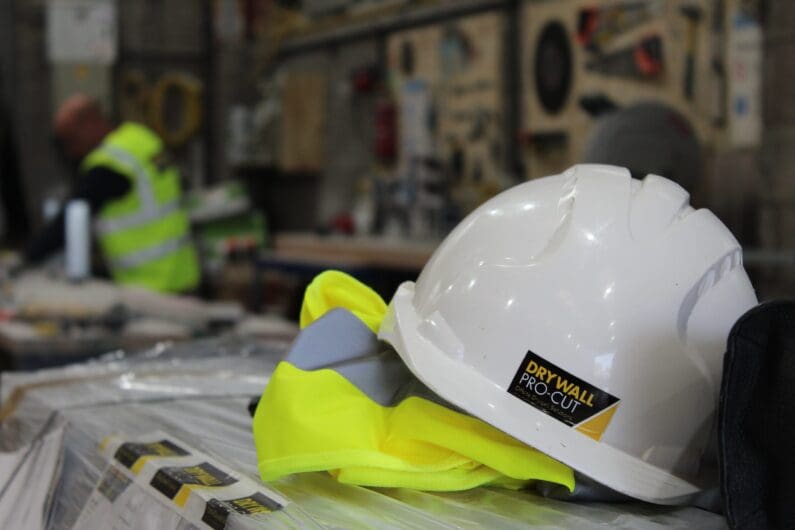
We are committed to quality and safety
Some large drywall contractors utilise over 100 people on site fixing because it is such a labour intensive operation.
In a fast moving project, for a specialist contractor, or a main contractor, to monitor and check all that is being installed can be a daunting task, even for the best organised teams.
It occurred to us that for us to improve how we control installation we need to take a more active role in standardising some of our operations on site.
Therefore, improving quality and ensuring we comply with the manufacturers recommendations.
Drywall’s repetitive nature, diverse crews, and varying interpretations create chaos.
However, making crucial ‘Core Four’ components – deflection heads, builders’ works openings, and door sets – where compliance is critical can reduce this chaos. Pre fabricating these items alone would de-risk a project substantially.
FAQs
What makes Drywall Pro-Cut the leading offsite drywall supplier in the UK?
Why should I choose offsite drywall components from Drywall Pro-Cut?
What are the benefits of offsite drywall manufacturing?
What types of prefabricated drywall components does Drywall Pro-Cut offer?
deflection heads, builders’ works openings, door sets, and more. Our patented solutions de-risk projects significantly.